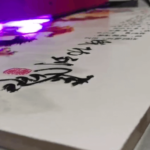
Multiple Effective Ways to Save More Water for Textile Manufacturing
- FninkJet
Willing to Diversify
Changing processes isn’t always easy, especially when textile companies have been doing things the same way for years with little or no other changes. However, it is crucial to remain open to the potential of water-saving technologies.
In fact, adopting an adapted or completely new process takes time and requires the approval of people at all levels of the company. However, the rewards for doing so can be substantial.
A textile aid for polyester processing saved more than 130 million liters of water in its first year of launch. It saves money and time by combining multiple polyester processing steps into one bath.
Another option is to seek out more sustainable products from suppliers, Sensil Water Care is an example. They developed pre-dyed nylon so textile industry representatives who bought it could steer clear of potentially outdated and water-intensive in-house dyeing processes. Sensil says the fabric can be resource-efficient while reducing water pollution.
It is becoming more and more obvious that the old-fashioned textile production process is very wasteful of resources. It’s not that corporate leaders are going to cancel them outright or outright, but hopefully they will at least be willing to explore different, more sustainable alternatives.
Pursue More Recyclable Options
More and more manufacturers are embracing the circular economy, and are exploring more avenues for recycling. Controlling water consumption in the textile industry in this way has the potential to have multiple positive impacts.
An EU-funded initiative called Waste2Fresh is a case in point. It is designed to use catalytic degradation for separation and extraction technologies to save water and reduce pollution.
“There is a problem with the way the industry uses water. Because of the chemicals in the water, the industry needs a lot of water and it pollutes the water,” said Ingun Grimstad Klepp, professor at Oslo Metropolitan University.
Statistics show that the textile industry consumes 100-200 liters of water for every kilogram of product produced. However, the recycling of water resources in this industry is not as simple as people think. This is because various processes during product processing can make water oily, corrosive, or have other undesirable properties. Therefore, it is critical that companies have a solid plan for removing contaminants before taking recycling measures.
In fact, the scope of recycling in textile factories can be more than just water. In a recent example, MIT researchers discovered how to make polyethylene from recycled plastic bags. “It’s more troublesome if someone throws plastic bags into the sea. But these bags are actually very easy to recycle, if you can make polyethylene into sneakers or hoodies, then ‘retrieve’ these The act of bagging and reusing it makes economic sense,” says Svetlana Boriskina, a research scientist at MIT.
Consider Using IoT sensors
The Internet of Things (IoT) has played an important role in providing better overall visibility to corporate decision makers. Leaders at Ohio-based Standard Textile saw the technology’s potential, and it worked as they worked to upgrade their smart sensor-based factories.
Company CEO Gary Heiman explained: “The Internet of Things has given us a much faster understanding of what we need to do. It has given us insight into what’s going on throughout the process, something we’ve never had before.”
The plant’s technology allows everyone to see how much water is left at the end of one production cycle, so workers can use the previous amount at the beginning of the next production cycle. The company also uses IoT to detect equipment failures, a strategy that also reduces water usage.
IoT can quickly resolve issues in production, such as leaking pipes or unturned faucets, which can lead to a rapid increase in a facility’s overall water usage. However, IoT sensors can target and solve these problems, and it can accurately remind the responsible person of different situations.
Understand the Variability of Water Demand
Minimizing water use in textile factories is actually more complicated than some initially thought. Because there are so many variables, this can make total consumption fluctuate greatly.
For example, knitting factories require an average of 10 gallons of water per pound of product, yet they actually consume between 2.5 and 45.2 gallons.
Also, when you compare fabric washing to dyeing, you’ll see that certain processes use more water than others. There are many mechanical factors, such as physical flow and agitation characteristics, that affect the total amount of water required for a step.
Company leaders who know roughly how much water each process step requires can check to see if the statistics match expectations. If not, it may be time to consider implementing new control processes to limit excessive water use.
There is no Single Option for Reducing Water Use in the Textile Industry
These tips are an excellent starting point for reducing water use in the textile industry. Before implementing at least one of these, however, manufacturing decision makers should take the time to assess their company’s existing processes and the associated resources they rely on. This will make it easier to develop a budget and set a timetable for meeting the company’s water sustainability goals.
Share:
More Posts
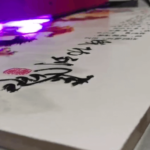
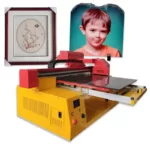
What are the Reasons for the Color Deviation of UV Flatbed Printers?
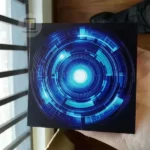
What is the Difference Between LED Flatbed Printer and Traditional Inkjet Printing
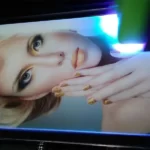
The Difference Between Printhead Cleaning and Pump Ink of Flatbed Printing Machine
Subscribe To Our Newsletter
No spam, notifications only about new products, updates.